“Is this insulin animal-free?”
In a future where major medications – like insulin, cancer treatments and life-saving vaccines – are grown from plants, such a question is valid.
Though the Canadian Food Inspection Agency has said, “There is no commercial plant molecular farming in Canada to date, and none is anticipated in the near future,” University of Guelph researchers disagree.
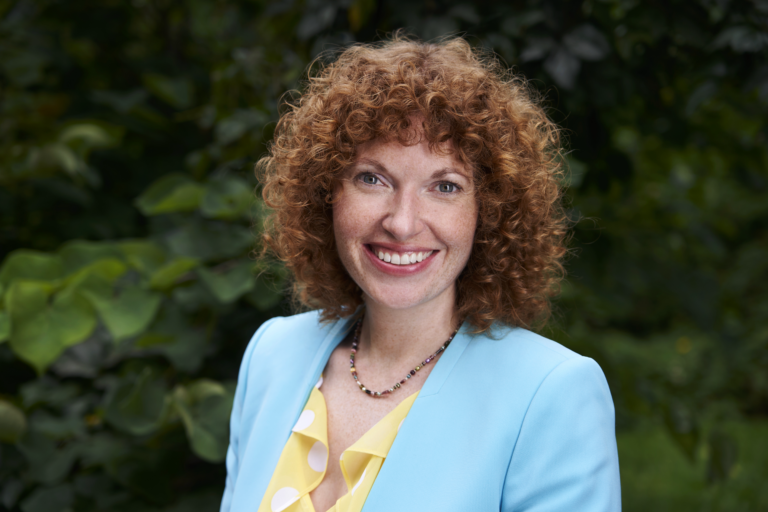
As Dr. Jennifer Geddes-McAlister, professor in the College of Biological Science puts it, there is no reason plants should not be making our drugs right now:
“In theory, it should already be happening,” she says. “Because the promise is there. The setup and infrastructure are there. The research is there. The biggest hurdle is reducing variability in drug production.”
These are the current aims of molecular pharming, the field that uses plants, rather than costly animal cells and materials, to produce our pharmaceuticals.
Plants could shorten pharmaceutical production times
U of G researchers have recently confirmed molecular mechanisms that could turn the visions of molecular pharming research into industrial and commercial realities.
In a recent study published in Plant Biotechnology Journal, the researchers investigated a plant-bacteria production system that produces trastuzumab, an antibody used in breast cancer treatment. Led by Geddes-McAlister and then-PhD student Nicholas Prudhomme, the study found key proteins and metabolites were produced during the process.
This gives manufacturers the molecular insights that could one day see plant-based drugs produced at a full industrial scale – good manufacturing practice (GMP) standards and all.
COVID-19 has exposed our need for vaccines to be produced quickly and at a mass scale. Plants have been identified as a promising way forward, able to shorten production times from months to days.
Cutting down costly animal media and materials – like fetal bovine serum, a main ingredient required to grow most cells, or even the chicken eggs used to create the flu vaccine – plant-based production systems are estimated to be only 68 per cent of the cost of current production methods. Research labs have been able to produce vaccines – like for the seasonal flu or COVID-19 – insulin, cancer treatments, hormones and even cosmetic products. They could even make medicine in space.
And, of course, plant-based drugs have appeal for other considerations: religious, diet and lifestyle preferences.
“The molecular side of research done at U of G gives a foundation to improve molecular pharming,” Geddes-McAlister says. “This project is quite exciting because it gives some suggestions and highlights as to how to make the production system better and more cost effective, with a higher production of drugs in the end.”
How does molecular pharming work?
Take a species of bacteria holding a gene that codes for the protein you want (the pharmaceutical), and infect a plant with that bacteria. The bacteria shares its DNA with the plant, and the plant-bacteria “factory” begins to create the drug.
In the case of the plant Geddes-McAlister’s team studied – Nicotiana benthamiana, a close relative of tobacco – the drug begins to collect in the leaves. The larger the leaves, the more drugs the plant can produce.
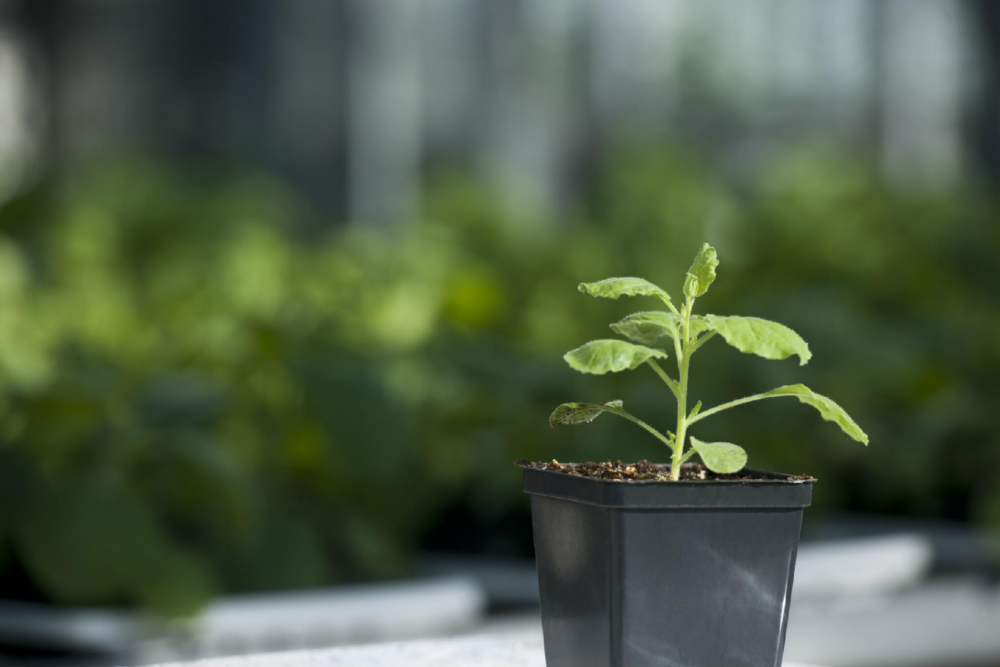
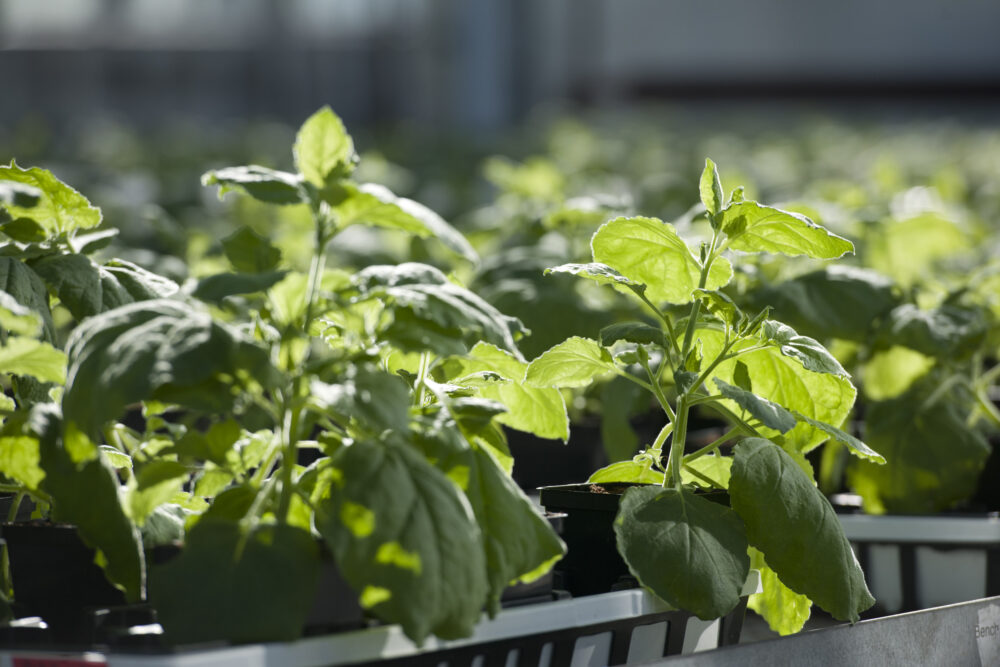
Nicotania benthamiana, a close relative of tobacco, used in the plant-bacteria “factory” system developed by PlantForm Corp. (photo by PlantForm Corp.)
Their partners at PlantForm, a company founded by U of G researchers in 2008, have developed the platform that the researchers investigated, the specific combination of plant, bacteria and drug.
In this setup, plants in greenhouses replace the more common paradigm: mammalian cells in culture dishes. The scale of production becomes much bigger, and the costs per drug much lower.
Geddes-McAlister says this isn’t the same thing as a GMO.
“It’s not a genetically modified system,” she says. “When you infiltrate the plants with the bacteria, you capitalize on a natural disease that occurs in plants in the wild. You’re facilitating that process, but it’s done through a vacuum.”
Another benefit to the method beyond cost savings and speed is reduced risk of allergens. Because animal cells add modifications to proteins, there can be unwanted immune reactions caused by the final product. There is less risk with the plant N. benthamiana – it doesn’t even produce pollen.
In Geddes-McAlister’s study, the team used innovative technologies associated with proteomics – the study of proteins in a biological system, and metabolomics – the study of metabolites produced by the plant.
They’ve found the enzymes that destroy the drugs before they can be harvested. Looking at the proteins and metabolites that appear also tells a story about what’s happening “under the hood” of the plant–bacteria system, so that each step may be improved upon.
“Proteomics and metabolomics give you new insight into how things are happening,” she says. “We wouldn’t have identified those enzymes that degrade the drug without looking at the proteins.”
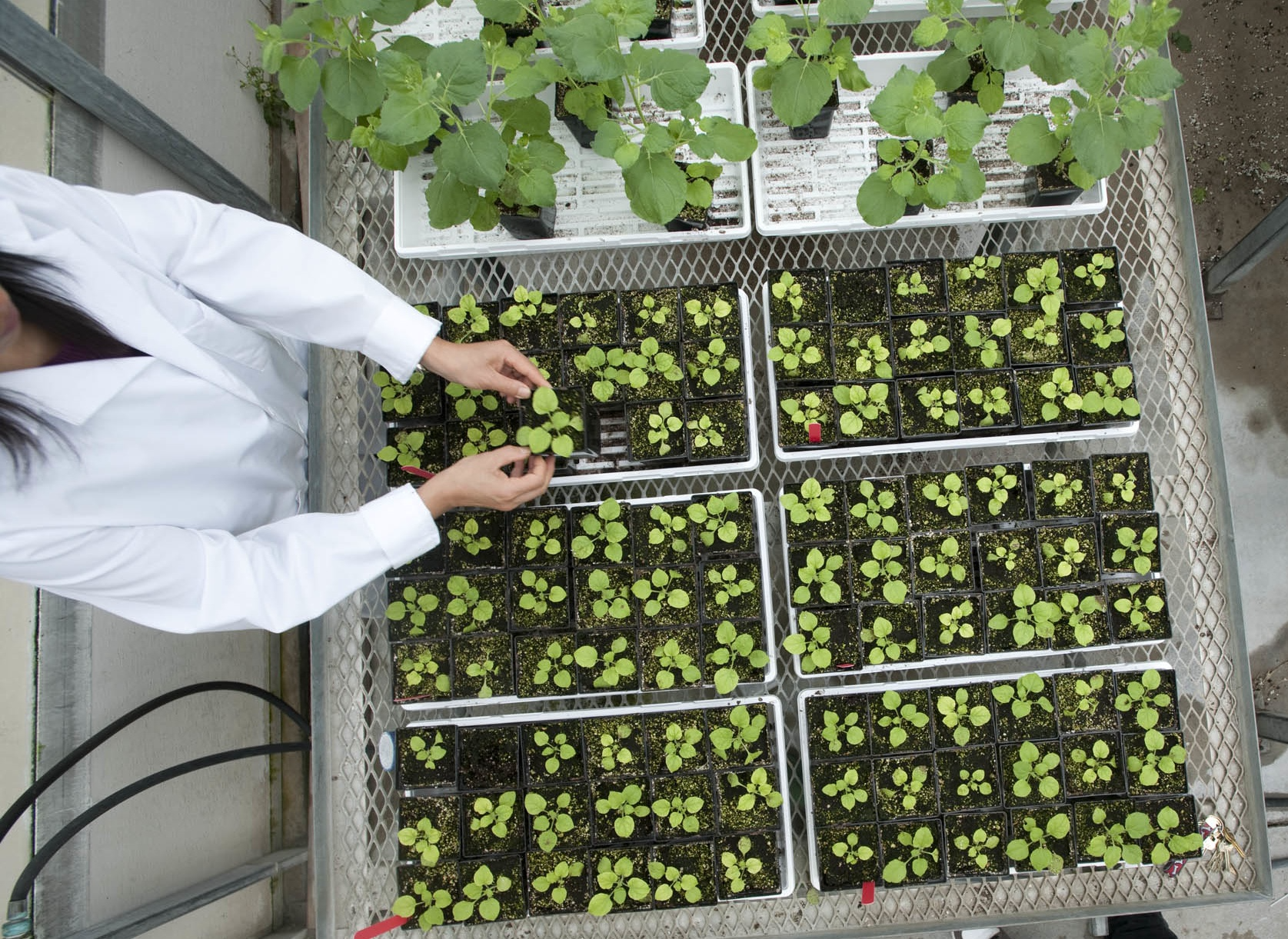
Photo by PlantForm Corp.
Bioreactor best for creating plant-bacteria ‘factory’
The team has also solved a crucial divide about the best method forward: whether to use a shake flask or a bioreactor when growing the bacteria.
Geddes-McAlister’s research has confirmed a longstanding hypothesis: bioreactors are better. Not only do they allow for higher-volume bacterial production with precise control over nutrients and conditions like pH and temperature, they seem to “prime” the bacteria to infect the plant quicker and to find the best locations in the plant. The plant, also, doesn’t seem to activate its defence system as quickly.
This is surprising for her team.
“I think the bioreactor method is beneficial because bacteria can get in the plants faster and produce more of the drug,” she says. “But it also causes the plant to not recognize the bacteria as quickly, so it doesn’t defend itself. That dual combination surprised me.”
The bioreactor breakthrough came with the help of fellow Department of Molecular and Cellular Biology professor Dr. Emma Allen-Vercoe, whose lab worked with PlantForm to investigate the scaling-up of bacterial production.
Solving this technical challenge clears one of the major hurdles that has prevented industry from seeing the full potential of molecular pharming.
Beyond bioreactors, other U of G researchers have made their mark. Dr. Lewis Lukens, Department of Plant Agriculture, collaborated with PlantForm to limit the defence mechanisms in host plants to increase drug production.
Plant-based drugs in the near future
The work left involves more questions about scaling up and timing.
“Instead of letting the plant sit for seven days to produce the drug, I’d like to see what happens when we let them sit for three days, and then collect,” Geddes-McAlister says. “In theory, this doubles the amount of material and halves the amount of time.”
Meeting industrial standards would also involve a study across different seasons – looking at the production of the drug, and how its qualities and quantities change over time.
Despite longer-term obstacles needing to be cleared, the day of plant-based drugs on our shelves seems like it is “anticipated in the near future.”
U of G is planting those seeds.
The study was made possible by Natural Sciences and Engineering Research Council of Canada (NSERC) Collaborative Research and Development Grant, an Ontario Graduate Scholarship, an NSERC Discovery Grant, MITACs, and through the Canadian Cancer Society (Atlantic Cancer Research Grant) and the J.D. Irving, Limited – Excellence in Cancer Research